Valves - gate valves and marine throttle valve
Valves - gate valves and marine throttle valve
Valves
To transport different liquids on the ship, many pipelines have been laid: for water and fuel, different gases. Some of them, by the way, actually transport energy - these are steam, compressed air, hydraulic fluid.
All these systems require shut-off valves - the common name for many different devices, valves, throttles, gates. It is needed in order to completely shut off the pipeline or regulate the flow of liquid or gas, connect and disconnect system elements and pipeline sections.
The word "valve", popular on land, is not used on ships - it is a "shut-off valve", and only a machine for lifting cargo is called a crane, but what you thought is a "rotary shutter". Only the "tap" remains. The fleet is the fleet.
The general name for any flow-blocking fittings is a valve . They are made of cast iron, bronze, brass, steel, stainless steel. The internal parts of the valve (valve mechanism) - spindle, valve seat, disc - are made of bronze, steel, rubber, or combinations thereof, depending on the operating conditions.
The most common types of valves are gate valves and butterfly valves.
Gate valves
They have always been the workhorses of the shipping industry, but after the introduction of throttle valves, they began to lose ground. However, when it comes to high temperature and pressure in s
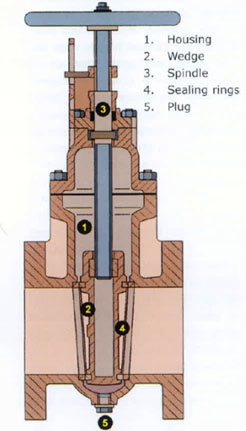
For larger diameters, or generally for severe service conditions, the valve is still the best choice. They can be used for almost any substance and at any temperature.
The design is a body with two flanges, inside which a wedge can move, blocking the flow completely or partially. The wedge design with metal seats provides a good seal. The saddles can be repaired on site with a special tool if necessary. There is usually a plug at the bottom of the body that allows you to check the tightness of the valve without opening it.
Body and wedge are available in cast iron, cast steel or bronze. O-rings are often made of bronze. But other combinations are also possible, depending on the type of liquid, the possible galvanic reaction.
Benefits of gate valves:
- 100% throughput;
- no back pressure of the working environment;
- two sealing surfaces;
- small face-to-face length;
- on-site tightness control.
Disadvantages:
- high headroom, especially if a hydraulic drive is installed;
- slow response;
- great effort on the shutter drive;
- heavy construction weight;
- severe wear of the seat surface on contaminated fluids.
Suitable for cooling water, water ballast, bilge systems, cargo (oil) systems, fire lines, etc.
Throttle valve
She 's a butterfly valve . Now the dampers are confidently crowding out the classics of the genre - latch valves. The design is simple and reliable, and the soft seat material ensures no leakage. The tremendous weight reduction of the valve over the valve and the disc rotation of only 90 ° (which is why the butterfly valve is referred to as the quarter turn valve with the ball valve) makes the throttle valve ideal for use in an engine.
The actuator (actuator) can be electric, pneumatic, or even hydraulic for large valve sizes. Working pressure range from 6 to 25 bar. The regular butterfly cannot be used with steam due to the soft seat material, but there are special models for steam.
Housing throttle marine use is usually made of malleable cast iron or spheroidal graphite iron. Valve discs are made of aluminum-bronze alloy or stainless steel. Vulcanized rubber saddles or replaceable rubber rings. The most commonly used nitrile butodiene rubber (NRB, or perbunan, bunan), which perfectly resists both fuels and lubricants and sea water, with an operating temperature of 80 °, or other types of rubber, with a temperature of up to 150 °. Teflon (PTFE) is used for particularly harsh conditions.
Up to DIN200 sizes, the disc can be turned manually using a lever. For large sizes, mechanisms are used.
Choke valves are best used in a horizontal position so that dirt build-up cannot damage the seat and stem.
But that's not all about valves - the main mechanisms for controlling the engine and its entire environment. In the next article, we will continue this fascinating topic.