Starting devices
Starting devices
A starting device is the general term for a piece of equipment with one or more contactors that allows the connection of a consumer to its main power supply.
Starting devices can also be used to limit the inrush current of a consumer to an acceptable value when connected to the main power supply. An acceptable value is one that does not disturb the proper functioning of the prime source of power like a generator as this would also disturb other equipment in the installation.
Limiting the starting current will also limit the starting torque of an electric motor. This may be necessary to protect for instance a delicate gearbox from the harmful forces of direct on-line starting.
Some examples of starting devices are:
1. direct on-line starters
2. star-delta starters
3. autotransformer starters
4. frequency converters
5. high voltage choke starters
1.1. Direct on-line starter
The simplest way of starting an AC motor is the direct on-line starter. With this device the starting time is minimal, the starting torque is maximal at full voltage but the voltage drop, also at other consumers, is maximal.
Values for voltage drop levels can be calculated when the starting data of consumers is known as well as capability data of generators. In general, a generator is able to supply a sudden overload of 50 % of its kVA-rating, resulting in a voltage drop at the generator terminals of less than 15%.
This allows another 5% voltage drop in the distribution network, in order to stay under the maximum allowed voltage drop of 20% during starting of a large consumer. The voltage drop is a result of the capabilities of the generator as the load on the driving diesel engine during starting is determined by the power factor, usually less than 0.4 during starting.
A diesel engine should be capable of handling a load step of 20% or more without a frequency dip of more than 10%, which should be recovered within 15 seconds. The minimum requirement for step loads on diesel engine generators is 33%. However, modern commonrail and constant pressure electronic injected diesel engines have some difficulty handling such step loads
Example direct on-line starter
Example of an engine room without local starter boxes.
Starters for these pumps are installed in MCC's (see below)
Example of a Motor Control Centre (MCC) where all starters for the engine room are installed.
The panel on the far left is for the connection of the incoming main power
1.2. Star/delta starters
Star-delta starting is a much used method as it is cost effective, uses proven technologies and is widely available.
An example of a star-delta starter is given below. For large motors, which require large contactors (K1,K2 and КЗ), these contactors can be supplied from the primary voltage instead of from the voltage transformer. The main contactors as shown will then be replaced by auxiliary contactors.
Star-delta starters reduce primary values as follows:
- starting current by 1.7
- starting torque by 1/3
- the load on the engine by 1/3.
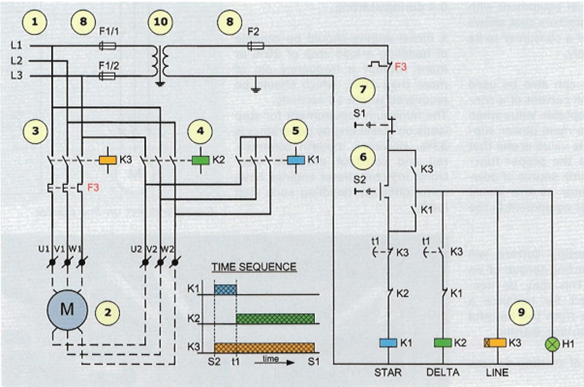
Example of star-delta starter
2. Electric motor
3. Contactor КЗ
4. Contactor K2
5. Contactor KI
6. Start button
7. Stop button
8. Control fuses
9. Time relay
10.Transformer.
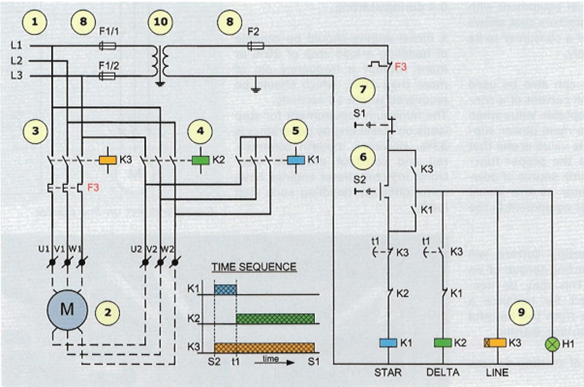
Example of Auto transformer starter
1.3. Auto-transformer starters
Auto-transformer starters are based on the reduced voltage starting method whereby the starting current is reduced in proportion to the starting voltage. The start torque, however, is reduced proportional to the voltage square. This means that this starting method can only be used for low torque (no load) starting. But when designed well the motor rating connected to this type of starter can be considerable, sometimes in the MW range.
An example of low torque, high power starting is a starter for a bow thruster where the propeller blades are put in zero position before starting. Autotransformer starters are normally provided with a number of secondary voltage tappings. This allows a change of starting voltage, and with that of starting torque, during commissioning a system. The values of these secondary voltage tappings are normally in the range of 55 -70 % of nominal voltage. Lower values would increase the starting time, higher values would increase the starting currents. Both effects are undesirable.
1.4. Frequency convertersFrequency converters and other electronic control devices can control current, power and torque of an electric motor. They limit the starting conditions on the generators, arrange the maximum performance of the consumer.
1.5. High voltage choke starter
As for low voltage, for high voltage starters the direct-on-line (DOL) type is the most cost effective. But starting direct on-line could cause too much peak-load on the generators or driven equipment. In that case the current can be limited by inserting a choke in the supply line to the motor. This choke, when designed properly, will reduce the starting current. As the torque will also be proportionally reduced, the effects of in serting a choke must be carefully evaluated to avoid stalling of a motor during start-up.
An example of a high voltage choke starter
Starter box and remote control of turning gear, and starter box of pre-lubricating pump